Aramids
The most common organic fibres used for reinforcements are the aramid, or aromatic polyamide fibres, with Kevlar® and Twaron® currently the major brands. Aramid fibres were originally used as reinforcements for tyres, belts, and other rubber-related goods, but today they are extensively used in high impact applications, including ballistic resistance.
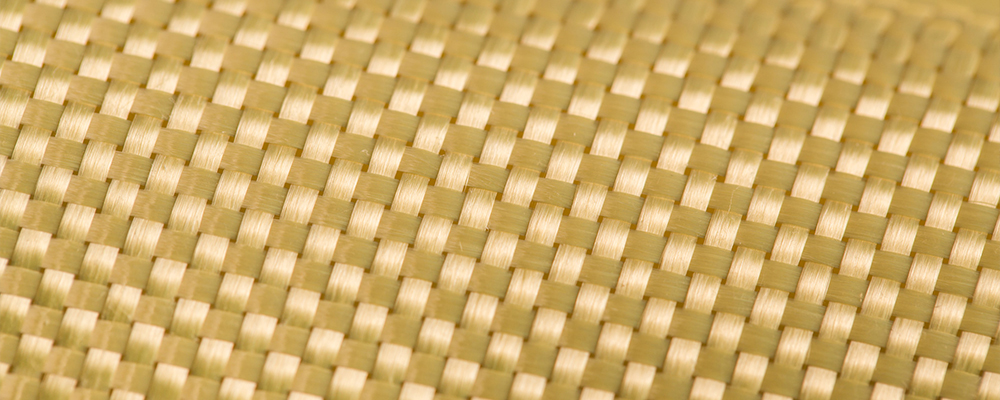
Aramid fibres are around 40% less dense and intermediate in strength between glass and carbon fibres. The specific strength of aramids is comparable to carbon fibre, and the specific modulus is higher than glass but not as high as the outstanding specific modulus of carbon.
The failure of aramid fibres is unique in that when they fail, the fibres break into small fibrils, which are like fibres within the fibre, so aramid fibres fail by a series of fibril failures rather than a brittle failure like carbon and glass. This unique failure mechanism of aramids is responsible for their high strength and high toughness; however the fibrils do not have the same resistance to compression forces, therefore aramid fibres rarely used when compressive force resistance is required.
Advantages
- Tough material
- Low density
- Excellent tensile strength
Limitations
- Lower resistance to compressive force
Applications
- High-strength cloth, e.g racing boat sails
- Protective clothing and gloves
- Ballistic protection
- Bullet proof vests
- Armour for ships and combat vehicles
- Leading edges of aircraft wings
- High performance pressure vehicles
Techinical Details | ||||
---|---|---|---|---|
Density (g/cc) | Tensile Strength (ksi) | Tensile Modulus (Msi) | Elongation to Break (%) | |
Aramid (high toughness) | 1.4 | 523 | 12 | 4.0 |
Aramid (high modulus) | 1.4 | 580 | 19 | 2.8 |
Aramid (ultra-high modulus) | 1.5 | 494 | 27 | 2.0 |